IFUS: Individual Heat Supply with Integrated Fog Unit System
Project IFUS offer new technological solution of flue gas purification for small capacity biomass boilers, which is intended to reduce emissions and improve energy efficiency (till 20%), comparing with traditional solutions. The main idea for this solution is to create fog effect zone in the equipment of flue gas purification, thereby reducing emissions of small particles (PM 10, PM 2.5) and environmentally harmful gases. Fog zone properties in the joint of pollution will be considered also using electric and electromagnetic field. The main project activities include the creation of experiment plan for the process research of heat and mass exchange in the experimental equipment, the creation of mathematical model and coincidences comparison of the results with experimental data, measurements for determination of emissions reduction and energy efficiency improvement, using experimental equipment. Identification of technological solution will be done for pH level regulation during flue gas purification, to prevent risks of corrosion, and purification of pulp, which has emerge during flue gas purification. Finally process analysis of influencing parameters will be carried out, to be possible to improve performance of equipment. Main project result – prototype will be developed for equipment of flue gas purification, which is for emission reduction of small capacity boilers. The project aim is to develop new equipment solution of flue gas purification for combustion equipment of small capacity boilers, reducing emissions (about 80%) and increasing energy efficiency (about 20%), comparing with traditional solutions.
PROJECT REALIZED AT:
SCIENTIFIC LEADER OF THE PROJECT:
Dagnija Blumberga
PROJECT FUNDED BY:
European Regional Development Fund
PROJECT DURATION:
From 1st April 2017 until 31st March 2020
PROJECT BUDGET:
595 843,79 EUR
PUBLISHED:
17.02.2017.
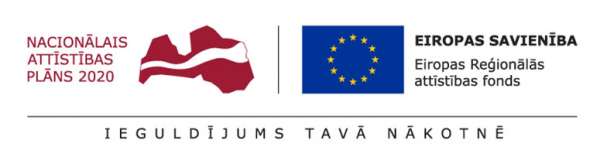
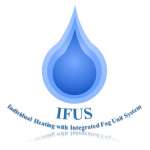
NEWS:
The project “Individual Heat Supply with Integrated Fog Unit System (IFUS)” is working on the transfer of the Intellectual property license agreement between 01/01/2020 and 31/03/2020.
The license will govern the legal relationship between the user and the developer of the engineering solution package, which includes use restrictions and distribution rights, copyrights and warranties. The transfer of the intellectual property license agreement is planned to be implemented during the project follow-up period, no later than 31/12/2023.
The current Licensing Strategy Paper describes the current commercialization of the technology in connection with the implementation of the Ecodesign Directive, providing market research with feedback from merchants (potential licensees) that would allow the intellectual property licensing agreement to be transferred during the project follow-up period until 31/12/2023, and highlights key aspects of the licensee recruitment process.
The Intellectual property license agreement will be concluded with the licensee, which will be determined by public auction in accordance with the laws and regulations governing the organization of the auction at Riga Technical University, whereby the licensor will receive the maximum price for the developed engineering solution package.
Posted on the website: 23.03.2020.
The project “Individual Heat Supply with Integrated Fog Unit System (IFUS)” has published two publications on the results of a set of experiments submitted for publication in international journals indexed in the Web of Science and SCOPUS databases.
- Link Between Multivariables of Heat and Mass Transfer in a Scrubber. Case Study: Fog Unit
- Article summary – Combustion processes are one of the major sources of air pollution. The research uses a new, innovative flue-gas cleaning technology – a fog unit. Its purpose is to purify the flue gases produced by households. In the European Union, including Latvia, from 2020 a directive setting emission and efficiency limit values for combustion plants in households comes into force. The main purpose of this study was to determine which performance parameters have the greatest effect on the power (QMA) of the fog unit. Statistical processing of experimental data made it possible to obtain regression equations describing QMA, water temperature at the outlet of the fog unit (tw2), and gas temperature after the fog unit (tg2). These values represent the effectiveness of the fog unit.
- Small Scale Pellet Boiler Gas Treatment in Fog Unit
- Article summary – The purpose of the study is to experimentally determine the characteristics of the operation of a fog unit and its effect on particulate matter trapping. Laboratory equipment – a fog unit – has been created for carrying out experiments. It is suitable for use with pellet boilers with a nominal capacity of 10 to 30 kW. The paper deals with the influence of parameters on the significant changes in the indicators that are important for PM reception: the contact surface of the injected water and flue gas; the contact time of droplets and gases in the fog unit; and the residence time of the droplets in the fog unit. There is a high correlation between experimental and calculated data (the adjusted coefficient of determination (R2) is 85.32%).
Posted on the website: 27.02.2020.
The project “Individual Heat Supply with Integrated Fog Unit System (IFUS)” collects experimental data at three boiler capacities (10 kW, 20 kW, 30 kW) and nozzles (MPL 1.51, MPL 1.12, MPL 0.77) used to obtain the data set to be analysed. The data analysis program Statgraphics XVII performed experimental data analysis to determine what parameters affect the capacity of the fog unit and the efficiency of particulate matter (PM).
Regression analysis was performed to determine the parameters affecting the capacity of the fog unit, in which the dependent variables are:
-Flue gas temperature at inlet (tg1) and outlet (tg2);
-Water temperature at inlet (tw1) and outlet (tw2);
-Flue gas moisture content at inlet (ω1) and outlet (ω2);
-Wet flue gas flow (Vmg);
-Amount of water sprayed (G);
-Injected water – flue gas ratio (g/Vmg);
-Diameter of sprayed water droplets (dd0);
-Oxygen concentration in the flue gas (O2);
-Flue gas velocity at inlet (ug1) and outlet (ug2);
-The amount of water sprayed per unit cross-section (g/SMA).
The most important factors affecting the capacity of the fog unit are: tw1, dd0, g/Vmg, G, tw2, Vmg.
Regression analysis was performed to determine the parameters affecting PM reduction efficiency, where the dependent variables are:
-tg1, tg2, tw1, tw2, ω1, ω2, Vmg, G, g/Vmg, dd0, O2, ug1, ug2, g/SMA;
-injected water – droplet diameter ratio (g/dd0);
-surface formed by injection droplets in the fog unit (Fdrop);
-concentration of particulate matter before the fog unit (PM before)
The most important factors that influence the PM reduction efficiency of the fog unit are: tg2, tw2, ω2, Vmg, G, g/Vmg.
The study is also featured on LTV1 broadcast “Environmental Facts”. The storyline of the show about air pollution can be found here.
Posted on the website: 30.12.2019.
Within the framework of the activity 3.2, a program was developed, which includes a calculation model to describe the operation of the fog unit. The program is based on a pre-built mathematical model in the Excel environment (activity 1.3), which has been refined and transferred to another environment, facilitating faster calculations. Program written in PYTHON 3.7 using Visual Studio 2019. It includes the calculation of the thermal-physical parameters, the auxiliary equations and the calculation of changes in the main parameters. The main parameters, whose changes are considered in the model, are: injected water temperature, temperature of the flue gas, diameter and velocity of the water droplets, concentration of particulate matter and moisture content of the gas. Using the model data obtained, the heat capacity of the fog unit was also calculated.
The experimental data set includes measurements at three different boiler capacities (10 kW to 30 kW), injected water temperature (20 – 40 oC) and each water injection nozzle. Various injected water flow rates in each mode (45 l/h to 342 l/h) were tested, as well as the effect of oxygen concentration on the flue gas parameters.
Testing of the developed model takes place using data obtained from experiments as input data for calculation. The obtained results are summarized and compared with the data of the corresponding experiment at the beginning and end of the experiment to evaluate the correspondence of theoretically obtained parameters to the real situation. Reviewing the results obtained helps to improve and refine the model.
Posted on the website: 26.11.2019.